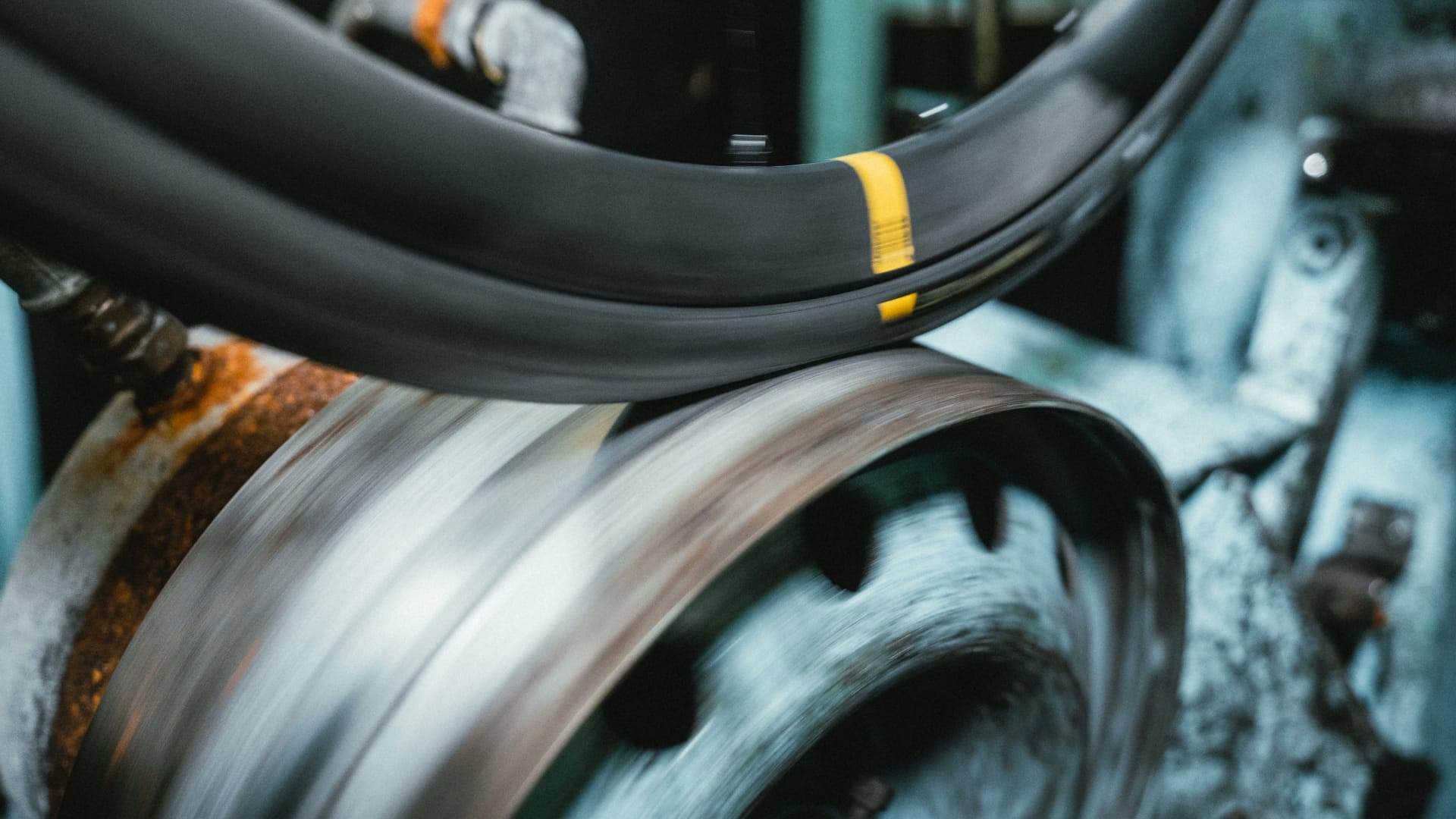
ラボテスト
マヴィックのラボテストの重要性
信頼性はマヴィックにとって不可欠な価値観です。マヴィックのコンポーネントの堅牢性は、純粋な性能よりも常に優先されます。マヴィックを使用すれば、ホイールの心配をすることなく、ライディングに集中することができます。
1993年、私たちは静的測定ラボを拡張し、動的測定器を導入することを決定しました。
今日、マヴィックのホイールをフィールドでテストし、販売するためには、ラボでのテストが欠かせません。さまざまなラボテストのおかげで、各ホイールの精度と強度をチェックすることができるのです。
その目的はシンプルです。サイクリストやマウンテンバイク愛好家に、信頼性が高く、耐久性に優れ、試行錯誤を重ねたモデルを提供することです。
抵抗テスト、衝撃テスト、耐久テスト......すべてがチェックされ、解剖され、限界まで追い込まれる。このテスト期間中に、欠陥や異常が発見され、私たちのチームによって修正されます。
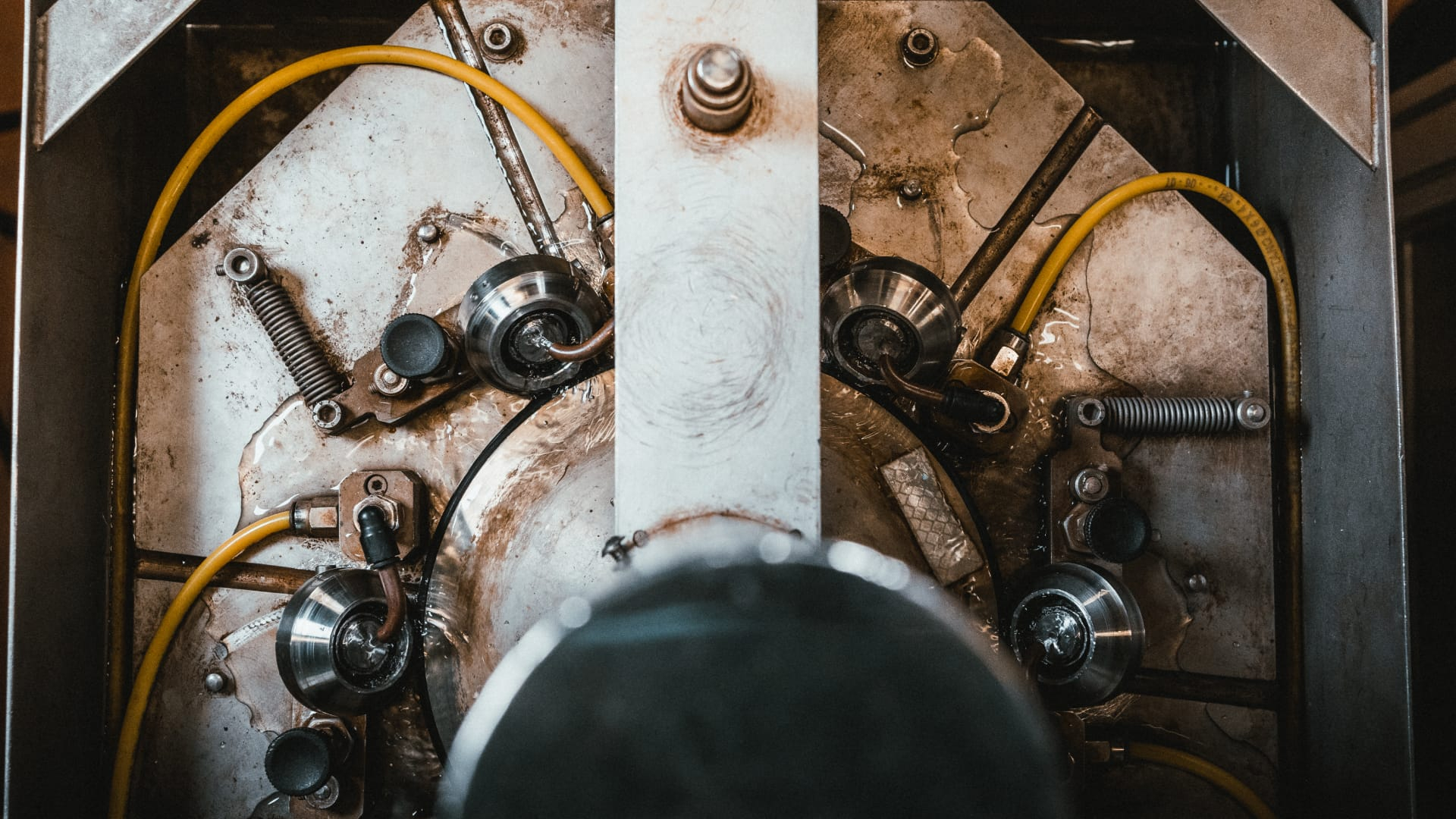
可能な限り設計段階に近いテスト
フレンチアルプスの中心、アヌシー近郊のシャバノに位置するマヴィック・コンピテンス・センターには、私たちの製品が設計・開発されるすべての施設があります。
同じ敷地内には、さまざまな評価ラボもあります。合計175m2以上が静的試験に、360m2が動的試験に使用されています。
機器を限界まで高める社内ツール
自転車業界において、テストのための特別なリソースと高度なツールが集中していることは、他に類を見ない。
マウンテンバイク、四輪バギー、オールロード、ロードバイクなど、あらゆるモデルをテストしています。合計で約47のテストを実施し、ホイールが自転車に装着されたときに受ける可能性のあるすべてのストレス(およびそれ以上)をシミュレートしています。
時速70km以上での7000kmの走行、-10℃から+70℃までの温度、300kgの荷重に対する耐性......衝撃、剛性、抵抗テスト、正面または側面の耐久ベンチ......各プロトタイプは仕様に従わされ、あらかじめ課された基準のリストを満たす。
最後に、"実験室でのテスト "段階を通過したホイールは、フィールドでフィーリングを確認される。ラボを出た各サンプルは、私たちのチームやアスリートたちによってテストされ、私たちの山々が提供するのどかで厳しい環境を利用します。
柱:パスカル・ランポン
1995年以来、評価・品質技術者として活躍するパスカルは、マヴィック・ラボテストの柱の一人です。これまでに5,000本以上のホイールが彼の手に渡り、新しいモデルのテストには数百時間を費やしている。
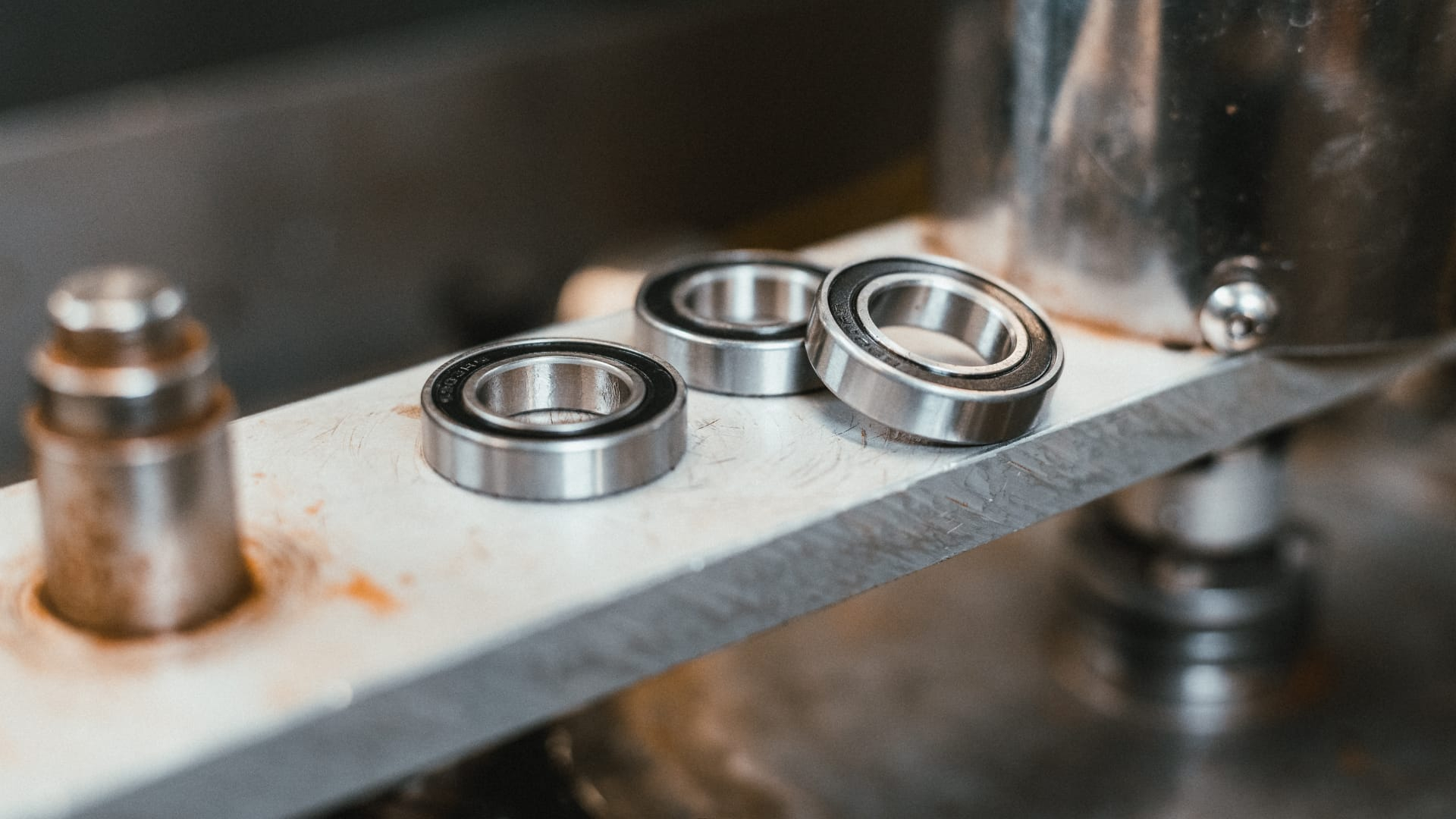
抵抗テスト
ベアリングの品質、ブレーキング、ショック...マヴィックラボで実施される主な抵抗テストは、機材の性能を証明するものです。
ベアリングテスト
私たちが選ぶベアリングはすべて、厳格な仕様に従っています。私たちはそれらをテストし、寸法を測定し、継続的に品質を評価します。
私たちはカートリッジ・ベアリングのシールの品質を測定するテストベンチを開発しました。これは、私たちがベアリングに対して実施している数多くのテストのひとつです!
ブレーキテスト
ブレーキング・ベンチは、スポーク・ハンガーからベアリングに至るまで、ホイールの強度をテストするために使用されます。
スケートでもディスクでも、自転車やマウンテンバイクのブレーキングは非常に高い応力を発生させ、ブレーキングによって生じる非常に高い摩擦による発熱や熱のレベルは言うまでもありません。
この測定ツールは、0~70km/hの間をノンストップで交互に750回のブレーキ操作を連続して行うことができます。
衝撃試験
ホイールは、大きな衝撃(道路の穴、舗装、木の根、岩など)を受けると変形します。その安全性と強度を保証するためには、応力下での変形を測定することが重要です。
ホイールは壊れたり、外れたり、変形したりしてはならない。ライダーがコントロールを維持し、可能な限り転倒を回避できるよう、衝撃を吸収しなければならない。これらのテストはUCIルールに従って標準化されているが、マヴィックでは最悪の状況を想定し、測定値を150%まで引き上げている。
強度試験
気候試験、衝撃試験... マヴィックのラボでは、最先端の耐性テストが実施されています。
気候試験
マヴィックのカーボンホイールはすべて、航空機器に匹敵する処理を受けます。とりわけ、リムとホイールはクライマティックチャンバーに入れられます。ここでは、高熱(+70℃)と強烈な寒さ(-10℃)のサイクルが、0~100%の湿度レベルと組み合わされ、数日間連続して行われる。
その目的は、カーボンファイバーの経年劣化を促進し、張力の変化などを測定し、ホイールやリムがすでに数カ月から数年経過しているかのように、さらなる試験や測定を受けるための「準備」をすることである。
ハブのトルク試験
トーションベンチは、ハブやスポーク・ハンガー、ディスク・ハンガーの経年変化をチェックするために使用されます。ホイールの心臓部にかかるトルクを意図的に減少させます。
ハブは、最高のアスリートたちが繰り出す電光石火の加速や、転倒を避けるための最悪のコンディションでの急制動に耐えなければなりません。これを実現するため、マヴィックハブの最大限の長期耐性を保証するために、10万サイクル以上の高い負荷をかけています。
轍テスト
マヴィックでは、ホイールクラッシュを完璧な安全条件でシミュレートするための特別なマシンを設計しました。
その目的は、重量、スピード、角度などの基本設定を常に同じにしながら、パラメーターをコントロールし、さまざまな結果を比較できるようにすることです。このようにして、私たちのホイールが極度の衝撃や変形に強いことを保証することができるのです。
これにより、軽量性、修理性など、他のすべてのパラメーターを考慮しながら、通常の使用において最悪の扱いに耐えるホイールを設計し、組み込むことができるのです。
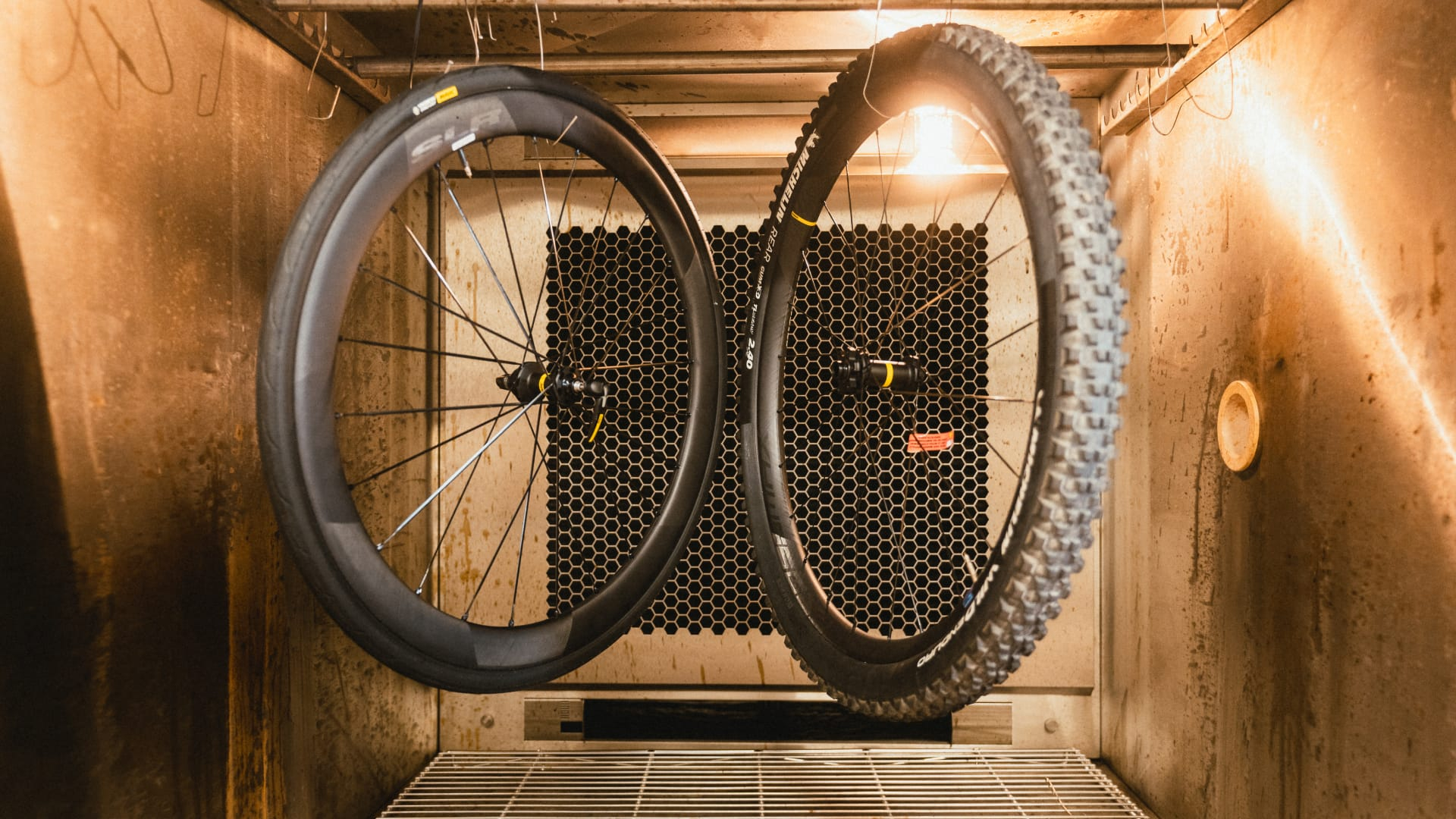
持久力テスト
ダンサーシミュレーション、正面または横方向の耐久性... マヴィックのラボで行われる耐久テストは、まさに限界に挑むものです。
ダンサー耐久テスト
疲労ベンチでは、アルプスの峠を非常に長く登るような500kmのノンストップ登山をシミュレートします。他のラボテストと同様、このテストはフィールドでの測定に基づいています。
ホイールにかかる横方向の応力とリアハブにかかるねじり応力が加算されます。
これにより、ホイールの構成部品の経年劣化を短期間でチェックし、必要に応じてパラメータや構造を変更することができる。
フロントエンド耐久試験
ホイールの経年変化に対する耐久性をテストするため、実験室のベンチでこのテストを実施し(時速70kmで7,000km、数日間)、その後、実際のコンディションでのフィールドテスト(マウンテンバイク用ホイールで5,000km、ロード用ホイールで10,000km)を行います。
横方向耐久試験
ホイールを水平に取り付けたリムに25kgのバラストをのせ、時速50km近くで連続回転させる。最初の300kmが重要だが、ハブ、スポーク、リムに負担のかかるこの構成で1000kmまでテストを行った。